Table of Contents
Monitoring circuit temperature in industrial production processes is extremely important. Temperature plays a critical role in ensuring the safety and stability of industrial circuits, without which production may come to a halt. Effective monitoring of temperature hence becomes vital, especially in circuits where overheating can cause severe damage. A reliable temperature monitoring system helps address this need through continuous and real-time surveillance of thermal conditions.
Challenges of Circuit Safety in the Industrial Sector
Several potential temperature-related issues may arise in industrial circuits. These include:
- Overheating Due to Increased Load: Heavy or unanticipated increases in equipment workloads can generate excess heat beyond tolerances, leading to damage if undiscovered.
- Localized Rise in Ambient Temperature: High surrounding environmental temperatures outside normal parameters have the potential to compromise component performance beyond specifications.`
- Malfunctioning Components Releasing Excess Heat: Faulty parts malfunctioning may release abnormal and excessive amounts of heat that require identification.
- Cable Fires: Prolonged high operating temperatures over extended periods pose a risk of insulation breakdown and ignition in cable runs, posing safety hazards.
For industrial customers, the main pain points regarding temperature monitoring are:
- Inability to Identify Temperature Anomalies on Time: Without a continuous real-time temperature monitoring system, detecting issues can be delayed, worsening repercussions.
- High Costs of Downtime Due to Failures: Unplanned stops and production losses caused by temperature-induced breakdowns impact productivity and revenue.
- Lack of Data for Root Cause Analysis: The absence of temperature logs and trend data hinders the diagnosis of recurrent faults and the determination of appropriate solutions.
These challenges point to the need for a reliable temperature monitoring system to preempt failures through early warning and ensure safe, stable circuit operations. Detailed data also helps determine long-term solutions.
The Importance of Temperature Monitoring Systems
A temperature monitoring system is a critical infrastructure for industrial circuits. Facilitating continuous thermal surveillance helps mitigate risks to safety and productivity. The following aspects highlight its significance:
Preventing Overheating
A temperature monitoring system instantly triggers audible and visual alarms whenever monitored equipment begins surpassing its normal operating temperature thresholds. This allows issues potentially leading to overheating, like excessive loading conditions, to be identified proactively before any thermal damage occurs. Precautionary measures such as reducing workloads, inspecting vulnerable parts, or performing diagnostics can rapidly be taken to circumvent failures and unplanned downtime.
Early Detection of Potential Failures
Through its round-the-clock and continual temperature surveillance at short intervals, the temperature monitoring system is adept at pinpointing anomalies indicative of more serious underlying problems at their early, emerging stages. Minor abnormalities, such as isolated hotspots developing due to loose connections, get immediately flagged, well before they can progress into major outages. This gives organizations timely alerts to either initiate pre-planned servicing routines or make contingency plans, eliminating disruptions to processes.
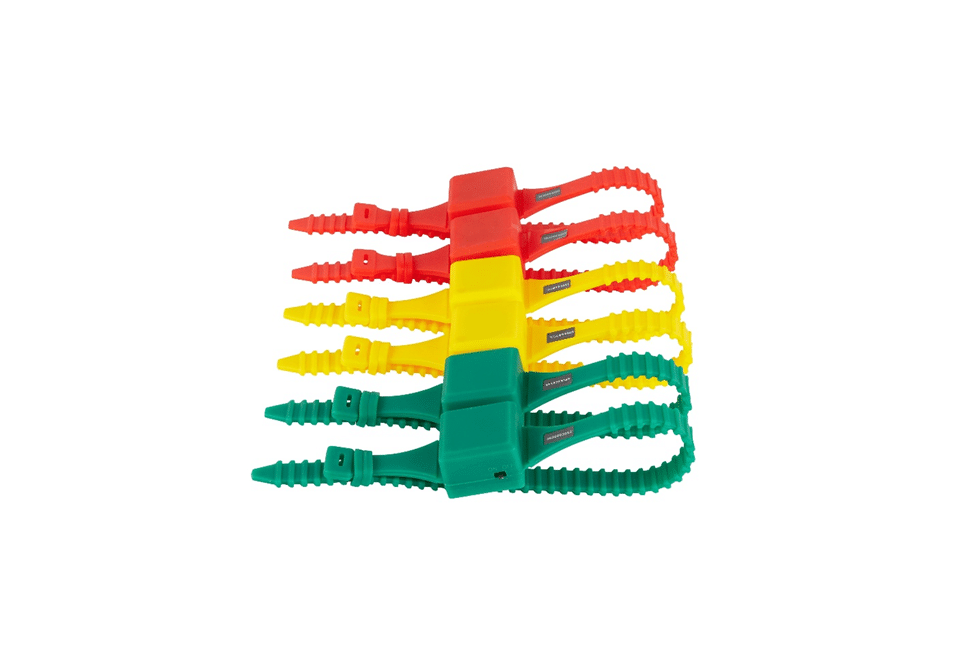
Product Highlight: TS-WTM Temperature Monitoring System
CHINT is a global leader in smart energy solutions. One such innovative product is the TS-WTM Temperature Monitoring System. It monitors the temperature of critical equipment across industries, including power generation, transmission, and distribution. Ideal for switchgear temperature monitoring, the system was designed with varied application scenarios in mind and with flexibility for customers. Some of its key objectives and application scenarios include:
- Ensuring Personnel Safety in High Voltage Environments: Tracking temperature levels of surfaces inside substations and switchgear allows workers to identify hotspots and avoid heat-related injuries during maintenance activities.
- Preventing Sudden Shutdowns of Movable Equipment: Constant thermal monitoring of circuit breakers used in movable substations helps detect internal overheating at early stages before it progresses to complete breakdown and outages.
- Optimizing Load Distribution: Minimizing equipment overload risks on transformers supplying power to large industrial facilities through accurate real-time visibility into thermal loads. Utilities can preempt failures and adjust loads as needed based on trends.
The TS-WTM Temperature Monitoring System works on the principle of wireless temperature sensor nodes. These nodes autonomously collect substrate temperature readings from multiple points at frequent intervals of 10 seconds. This high sensing frequency enables detecting even instantaneous thermal spikes or minor fluctuations that may indicate developing issues. Some key features of the system include:
- Wide Measurement Range of -25°C to 200°C: Allowing monitoring of equipment operating within this entire temperature spectrum typically seen in industrial settings. The high accuracy of ±1°C also ensures the reliability of readings.
- Long-Lasting Battery Life: The sensors are designed to function for 5-8 years, minimizing maintenance efforts.
- Robust Wireless Connectivity: Data transmission occurs over distances beyond 300m using secure 433MHz radio signals between the sensors and host monitoring system, even in areas with communication obstacles. This facilitates installation across broad facility premises.
Installation of the TS-WTM Temperature Monitoring System is a simple plug-and-play process requiring minimal time and effort. There are no trenching or cabling works involved, which could otherwise disrupt plant operations. The pre-calibrated sensor modules come pre-bundled and ready for immediate deployment. The key steps involve:
- Affixing Miniature Sensor Modules: The compact wireless devices are firmly mounted onto critical locations on equipment that are pre-determined to experience higher temperatures based on equipment layout/historical data.
- Synchronizing Devices: Each sensor is scanned by its unique identification number to establish communication between the nodes and the central monitoring control system hosting the backend software.
- Configuring Monitoring Settings: A few basic parameters, like temperature units, alarm thresholds, etc., are adjusted on the dashboard interface of the receiver console terminal to ready the system for autonomous surveillance.
Conclusion
Temperature monitoring systems play a vital role in ensuring circuit safety by preventing overheating-related failures in industrial production environments. Adopting the TS-WTM Temperature Monitoring System from CHINT helps gain real-time insight into thermal conditions across electrical infrastructure through continuous autonomous surveillance. Early visibility into temperature anomalies facilitates timely corrective actions, hence reducing downtime risks. The wireless, durable, and user-friendly technology enhances the stability of industrial circuits. Visit CHINT’s website for more details on the TS-WTM system and automation solutions.
Post Views: 376